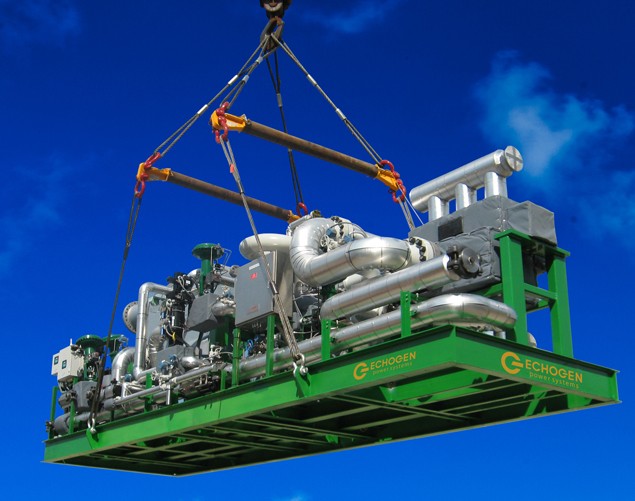
Waste Heat Recovery (WHR) systems are a proven technology that enables ship-owners to make better use of existing energy within the vessel’s full combustion cycle. By using waste heat from the engines, the efficiency of the combustion process can be significantly improved; manufacturers claim that savings in fuel consumption and fuel costs can be up to 10%.
This week, Fathom investigates the options owners and operators have for this impactful technology solution and its current status in the market.
How WHR Works
The fuel efficiency of ship main engines is currently approximately only 50% – only half of the energy content of the fuel is converted into electricity, while the rest is lost as heat energy. Up to half of this waste heat – around 25% of the overall energy content of the fuel – goes into hot exhaust gases which are then released to the atmosphere.
Modern marine engines – such as the super long-stroke MAN B&W S90ME-C9 type or the Wartsila RT-flex series – l use these exhaust gases to increase the power that the engine can produce. In a typical arrangement, the gases leaving the engine are passed through a turbocharger, which uses the energy of the gas to spin a turbine that forms part of an air compressor. This compressor increases the mass of air that flows into the engine, enabling large quantities of fuel to be burnt more efficiently.
However, the energy of the exhaust gas can be used in other ways. First, it can be used to spin a power turbine that produces electricity. Secondly, it can be used to generate steam which can then be used in a gas-fired boiler to meet onboard heat demands. Systems that achieve either or both of the above are labelled as Waste Heat Recovery (WHR) systems. WHR systems are typically located in the main engine room.
To make the most of the energy in the exhaust gases, some WHR systems include an exhaust gas bypass which channels part of the gas flow away from the turbocharger. This means that the temperature of the gas can be kept higher so that the WHR system can extract more energy from it.
In essence, the major advantage of WHR systems is to further increase the power generated for the ship without using more fuel.
WHR Installation Options
Ship-owners who wish to install WHR have three main options:
- (STG) Steam Turbine Generator
- (PTG) Power Turbine Generator
- (ST-PT) Steam Turbine-Power Turbine generator
The PTG system is the simplest and cheapest WHR system. A turbine is installed in the exhaust gas bypass, and this turbine produces electricity when the gas passes through. PTG systems are said to be able to recover 3-5% of the energy content of the fuel.
The STG system uses the exhaust gas for onboard heating. Part of the gas flow is directed through an exhaust gas bypass, which raises the relative temperature of the gas before it is used to generate steam for a gas-fired boiler. STG systems are said to be able to recover 5-8% of the energy content of the fuel.
ST-PT systems are suitable for ships that have high electricity demands, like containerships. In these cases, the power turbine and steam turbine form part of a combined system which produces both extra electricity and extra heat. ST-PT systems are said to be able to recover 8-11% of the energy content of the fuel.
In many cases, the ST-PT systems are expected to be able to supply the total electricity need of the ship as a standalone power source. ST-PT systems can also be run in parallel with auxiliary diesel generating sets, or a shaft motor or shaft generator.
It is expected that variants of these systems may also be available in future.
The best option will depend on just how much electricity the ship uses, its operational profile, and how much complexity the ship-owner and shipyard are willing to accept.
Financial Benefits
The financial benefits from using WHR can be significant, although these vary between technology providers and depend on the efficiency of the engine.
The engine manufacturer Wartsila states that their high-efficiency WHR system – which uses both power and steam turbines – could cut exhaust emissions and deliver fuel savings of up to 12%, with a return on investment of less than 5 years.
The global engineering, electrical and electronics company Mitsubishi Heavy Industries (MHI) claims that their WHR system for containerships saves 10% on fuel costs.
The engine manufacturer Man Diesel & Turbo is more conservative in their claims. They suggest energy savings of 4-11% for their WHR systems, depending on a range of factors such as the operational profile of the ship, electricity demand whilst at sea, and the power level of the engine.
However, for a ship which installs an ST-PT system, MAN Diesel and Turbo predict a payback of approximately 4.3 years, based on a conservative price for heavy fuel oil (HFO) of $US650/tonne.
For a ship-owner who keeps their vessels for 20 years, MAN states that this would equate to a $USD 36 million reduction in fuel costs.
The class society DNV has also made an independent estimate of payback times. In a study released in 2011, researchers concluded that a modern container ship, running on heavy fuel oil (HFO), could expect a payback period from a WHR system of around 8 years.
Case Study: Maersk
Maersk Maritime Technology has been an early pioneer with use of waste heat recovery technology.
Maersk Maritime Technology (MMT) have previously stated that high fuel efficiency can be expected from installing waste heat recovery technology, compared to other systems, onboard vessels.
“We are still wondering why we do not see more companies actually investing in the same [waste heat recovery] technology,” Jean Otto de Kat, senior director and head of innovation at MMT until the end of 2012, told trade press back in 2011.
“The cost of waste heat recovery systems could be $5 to 6 million dollars but if you take a long outlook life cycle analysis we do see that you get [to recover] the minimum payback value.
“So from an operational lifetime of 10 to 15 years it makes good sense to do this.”
Otto said that waste recovery systems can deliver up to 10% improvement in fuel efficiency for ships, resulting in a reduction in fuel consumption.
“You gain 10% [in fuel efficiency] from the heat loss that otherwise just move up the stack into the atmosphere,” said Otto. “It’s expensive. I think Maersk is the only one, or one of the very few which puts waste heat recovery system on their ships.”
All results are expected to vary depending on market conditions and fuel price. As fuel costs continue to rise, the technology continues to evolve and uptake is increasing.
According to the company, currently 32 Maersk containerships in total have been fitted with the technology since the 1980s, achieving reductions in fuel costs of 9%. Since 2008, WHR has been installed on all containerships that have been ordered and will be on the ten new Triple E ships currently under construction.
“It is the largest known CO2 reduction mean” states Ole Graa Jakobsen, who acted as project manager when the first of these systems was installed in 1988.
When a common slow steaming policy was introduced in 2009 “We had to find ways to optimize the output of waste heat recovery at low load” explains Ole.
This has traditionally been seen as technically challenging, as WHR systems only go into full operation above a certain engine load limit. However, Maersk has been able to successfully deploy a dual-speed strategy, where ships with WHR installed travel either above 21 knots or below 17 knots.
“Our experiences show that vessels with WHR still get more efficiency than standard designed vessels, even at low load” Ole says.
Case Study: Alfa Laval
As another sign of the growing uptake of this technology, Alfa Laval recently announced a waste heat recovery system that applies to auxiliary engines rather than main propulsion engines.
“Waste heat recovery systems after the main engines have proven lucrative for decades for many ship owners,” says Hans-Henrik Jensen, Alfa Laval Vice President, Marine & Diesel Division.
“Taking advantage of the waste heat from a ship’s auxiliary engines is the natural next step, which is now possible thanks to the Aalborg XS-TC7A.”
Alfa Laval announced the Aalborg XS-TC7A technology in December 2012 following two years of sea trials.
This system has a low weight for its output as well as reduced maintenance costs. The expected payback period is just 12 to 18 months.
Alfa Laval reports that a leading Danish ship-owner signed a contract in January 2012 to install the technology on 20 new builds as well as a substantial number of retrofits.
Jensen stated “The product has been very well received by the shipping industry, where many of the leading companies are investigating the possibility of installing the Aalborg XS-TC7A onboard.”
New WHR System on the Horizon
An innovative new waste heat recovery system is also set to enter the marine market.
GE Marine announced a new licensing agreement with Echogen Power Systems LLC in January that will see the Echogen system sold to commercial and military marine vessels worldwide.
The Echogen system is different to traditional systems due to its use of supercritical carbon dioxide (CO2) – heated CO2 that has properties of both a liquid and a gas –as its working fluid, rather than steam. This is said to make the system more compact and economical than a traditional waste heat recovery system.
Echogen said the product can operate efficiently in a broad range of exhaust temperatures, and the working fluid can be expanded for cooling or a combination of power and cooling.
“Converting energy that traditionally gets exhausted out of a stack into useful power allows the overall system efficiency to increase by up to 30%.” stated Brien Bolsinger, Vice President, Marine Operations at GE Marine, commenting on the impact of WHR on the engine system.
Echogen state that they have a goal of displacing steam as the power fluid of choice for engines under 50 megawatts in size.”
Echogen plans to test a 7 megawatt (MW) version of its system this quarter, and then develop 2MW and 0.4MW versions which it plans to start selling in 2016.
Conclusion
Shipowners have many options when it comes to WHR systems. There are multiple technological options and multiple providers. Given the scale of the expected fuel savings, this technology could prove to be a worthy investment and is certainly seeing increased take up.
For more news and tips on efficient shipping, please visit Fathom C-Tech
Image: Echogen Power Systems