In Part 3 of this series on shipping efficiency technology, we look at marine engineering and power systems technologies aimed at cutting operating costs, while at the same time reducing ship emissions. (Source: Wärtsilä)
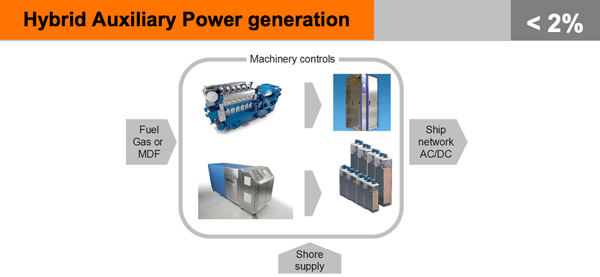
Hybrid auxiliary power system consists of a fuel cell, diesel generating set and batteries. An intelligent control system balances the loading of each component for maximum system efficiency. The system can also accept other energy sources such as wind and solar power.
Result:
- Reduction of NOX by 78%
- Reduction of CO2 by 30%
- Reduction of particles by 83%
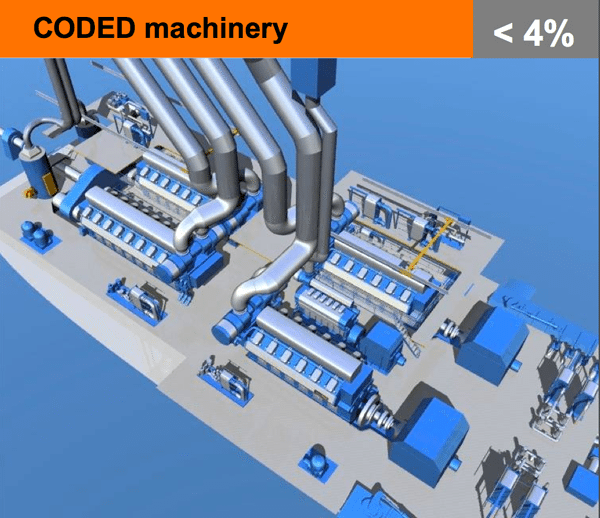
Combined diesel-electric and diesel-mechanical machinery can improve the total efficiency in ships with an operational profile containing modes with varying loads. The electric power plant will bring benefits at part load, were the engine load is optimised by selecting the right number of engines in use. At higher loads, the mechanical part will offer lower transmission losses than a fully electric machinery.
Total energy consumption for a offshore support vessel with CODED machinery is reduced by 4% compared to a diesel-electric machinery.
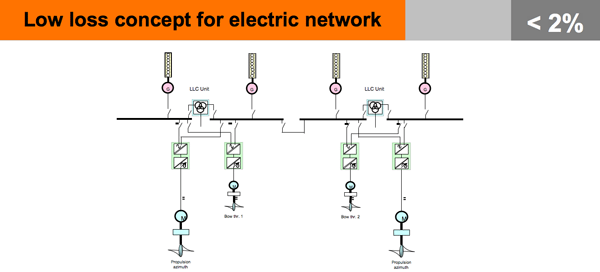
Low Loss Concept (LLC) is a patented power distribution system that reduces the number of rectifier transformers from one for each power drive to one bus-bar transformer for each installation. This reduces the distribution losses, increases the energy availability and saves space and installation costs.
Result: Gets rid of bulky transformers. Transmission losses reduced by 15-20%.
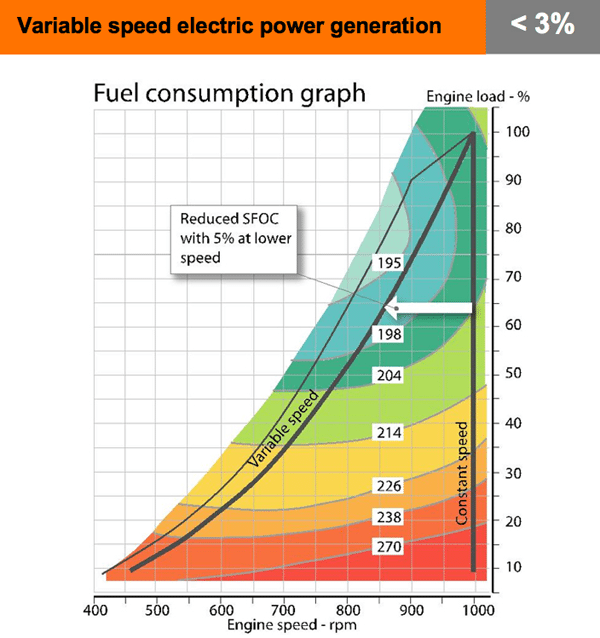
The system uses generating sets operating in a variable rpm mode. The rpm is always adjusted for maximum efficiency regardless of the system load. The electrical system is based on DC distribution and frequency controlled consumers.
- Reduces number of generating sets by 25%
- Optimized fuel consumption, saving 5-10%

Switching to LNG fuel reduces energy consumption because of the lower demand for ship electricity and heating. The biggest savings come from not having to separate and heat HFO. LNG cold (-162 °C) can be utilised in cooling the ship’s HVAC to save AC-compressor power.
Saving in total energy < 4 % for a typical ferry. In 22 kn cruise mode, the difference in electrical load is approx. 380 kW. This has a major impact on emissions.
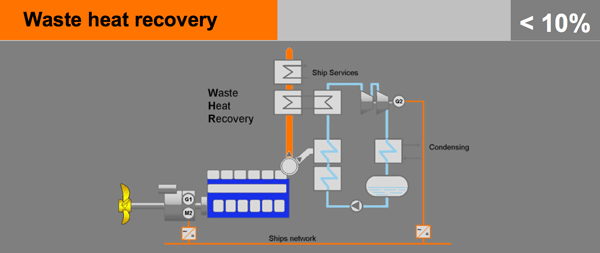
Waste heat recovery (WHR) recovers the thermal energy from the exhaust gas and converts it into electrical energy. Residual heat can further be used for ship onboard services. The system can consist of a boiler, a power turbine and a steam turbine with alternator. Redesigning the ship layout can efficiently accommodate the boilers on the ship.
Exhaust waste heat recovery can provide up to 15% of the engine power. The potential with new designs is up to 20%.
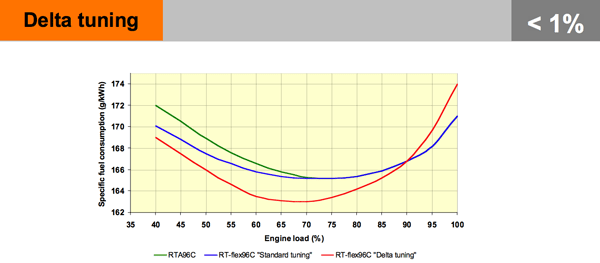
Delta tuning is available on Wärtsilä 2-stroke RT-flex engines. It offers reduced fuel consumption in the load range that is most commonly used. The engine is tuned to give lower consumption at part load while still meeting NOx emission limits by allowing higher consumption at full load that is seldom used.
Result: Lower specific fuel consumption at part loads compared to standard tuning.
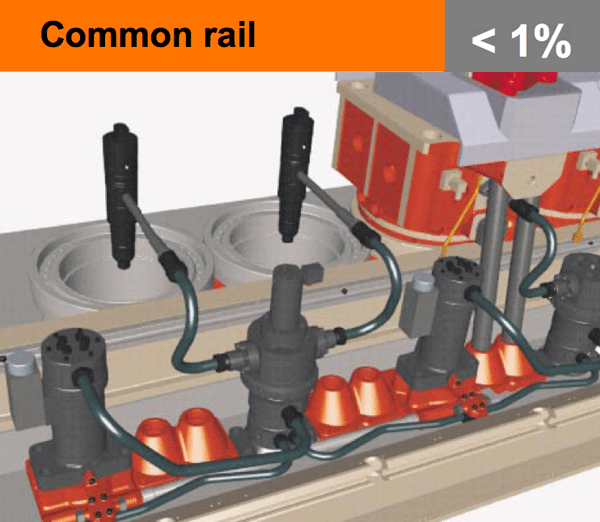
Common Rail (CR) is a tool for achieving low emissions and low SFOC. CR controls combustion so it can be optimised throughout the operation field, providing at every load the lowest possible fuel consumption.
Result:
- Smokeless operation at all loads
- Part load impact
- Full load impact
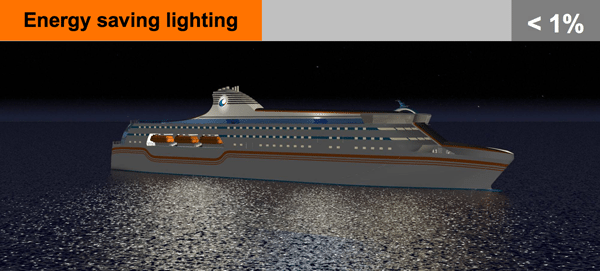
Using lighting that is more electricity and heat efficient where possible and optimizing the use of lighting reduces the demand for electricity and air conditioning. This results in a lower hotel load and hence reduced auxiliary power demand.
Fuel consumption saving: Ferry: ~1%
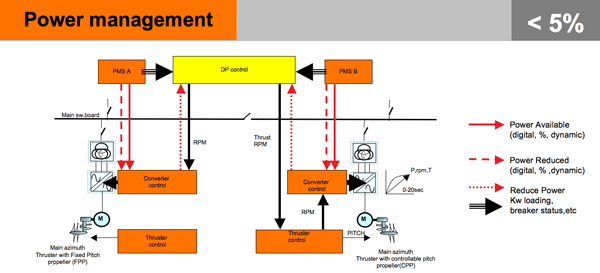
Power Management: Correct timing for changing the number of generating sets is critical factor in fuel consumption in diesel electric and auxiliary power installations. An efficient power management system is the best way to improve the system performance.
Result: Running extensively at low load can easily increase the SFOC by 5-10%. Low load increases the risk of turbine fouling with a further impact on fuel consumption.
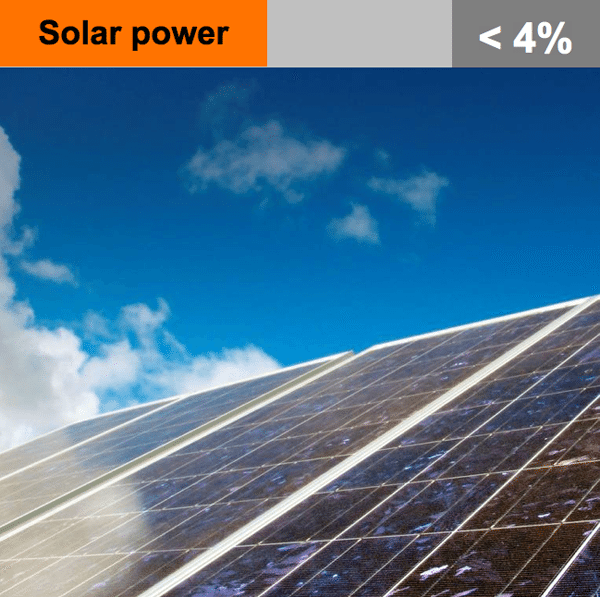
Solar panels installed on a ship’s deck can generate electricity for use in an electric propulsion engine or auxiliary ship systems. Heat for various ship systems can also be generated with the solar panels.
Depending on the available deck space, solar panels can give the following reductions in total fuel consumption:
- Tanker: ~ 3.5%
- PCTC: ~ 2.5%
- Ferry: ~ 1%
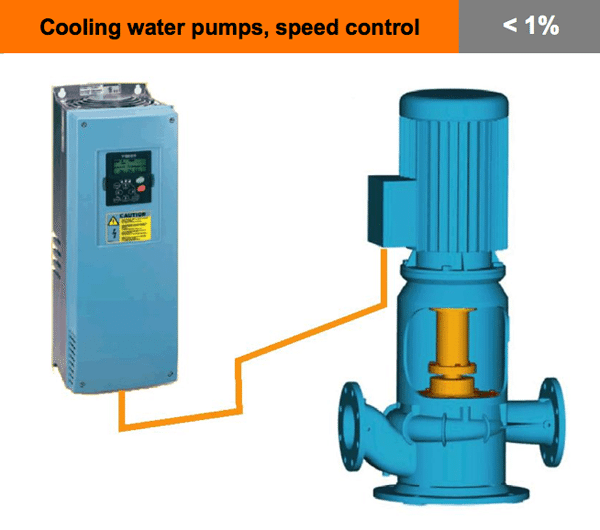
Pumps are major energy consumers and the engine cooling water system contains a considerable number of pumps. In many installations a large amount of extra water is circulated in the cooling water circuit. Operating the pumps at variable speed would optimise the flow according to the actual need.
Pump energy saving (LT only) case studies:
- Cruise ships (DE) 20-84%
- Ferry 20-30%
- AHTS 8-95%
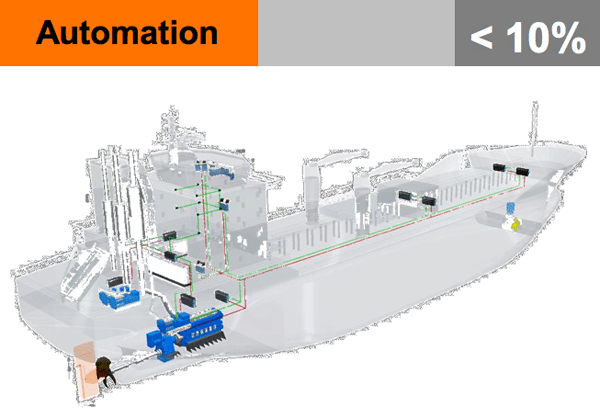
An Integrated Automation System (IAS) or Alarm and Monitoring System (AMS) includes functionality for advanced automatic monitoring and control of both efficiency and operational performance.
The system integrates all vessel monitoring parameters and controls all processes onboard, so as to operate the vessel at the lowest cost and with the best fuel performance.
Power drives distribute and regulate the optimum power needed for propeller thrust in any operational condition.
Engine optimization control, power generation & distribution optimisation, thrust control and ballast optimisation give 5-10% savings in fuel consumption.
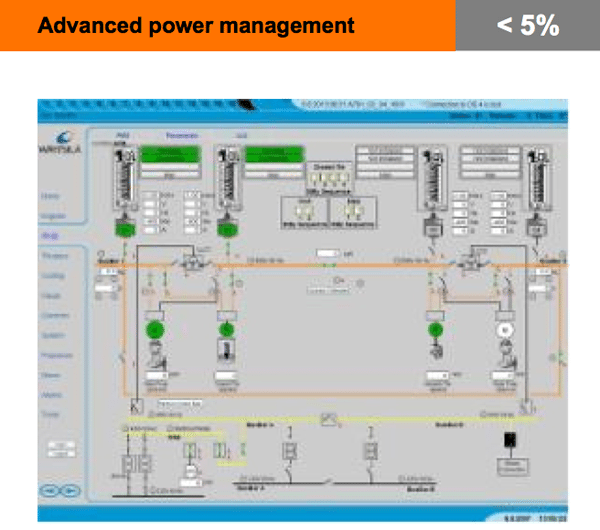
Power management based on intelligent control principles to monitor and control the overall efficiency and availability of the power system onboard. In efficiency mode, the system will automatically run the system with the best energy cost.
Reduces operational fuel costs by 5% and minimizes maintenance.
Part 4 will focus on specific Operational and Maintenance factors and their impact on a vessel’s efficiency.