While operating for Total E&P offshore Angola, the 1999-built Ensco DS1 drillship was running their blowout preventer (BOP) to the wellhead in 4,318 feet of water. Unfortunately, they forgot to open the blind shear rams while doing so.
After lowering the BOP 3,970 feet down, the hook load began to increase unexpectedly. With the blind shear rams closed, the riser had not been able to fill with water as it was lowered into the ocean, and as the hydrostatic differential continued to build, the pipe collapsed in on itself.
The following images were sent to us from an anonymous gCaptain contributor:
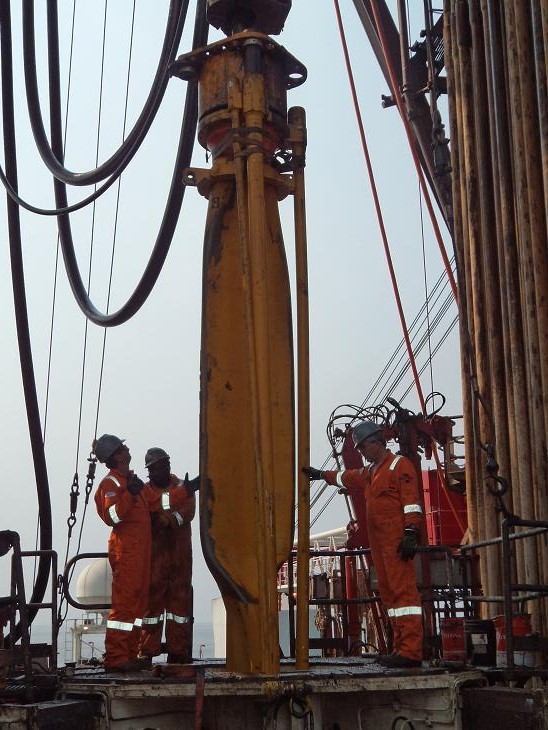
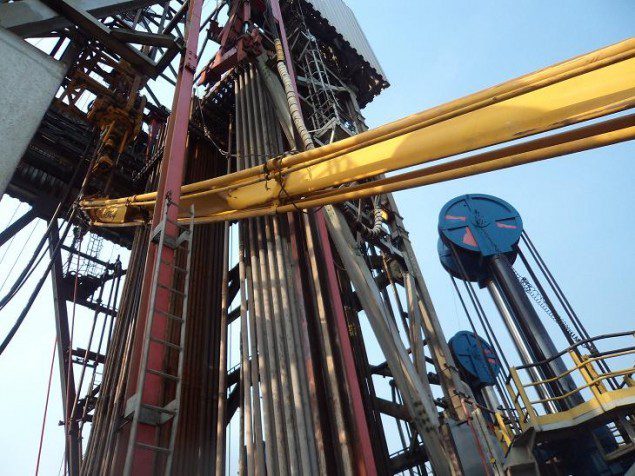
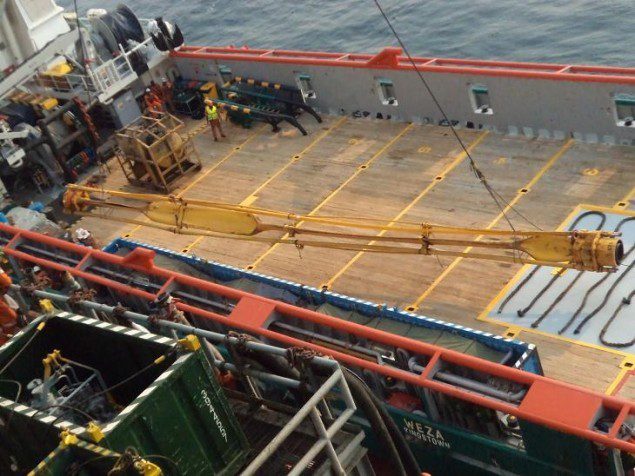
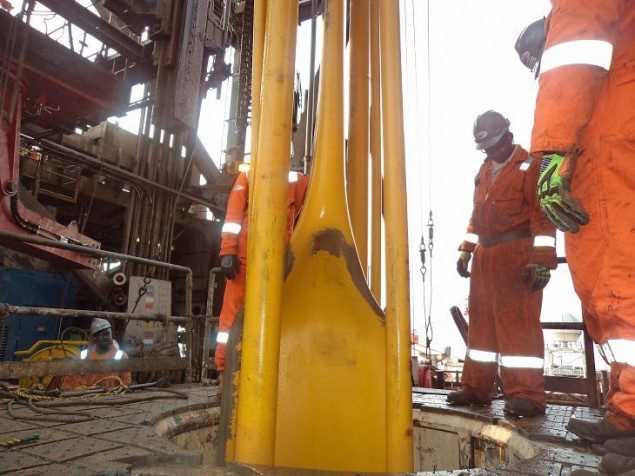
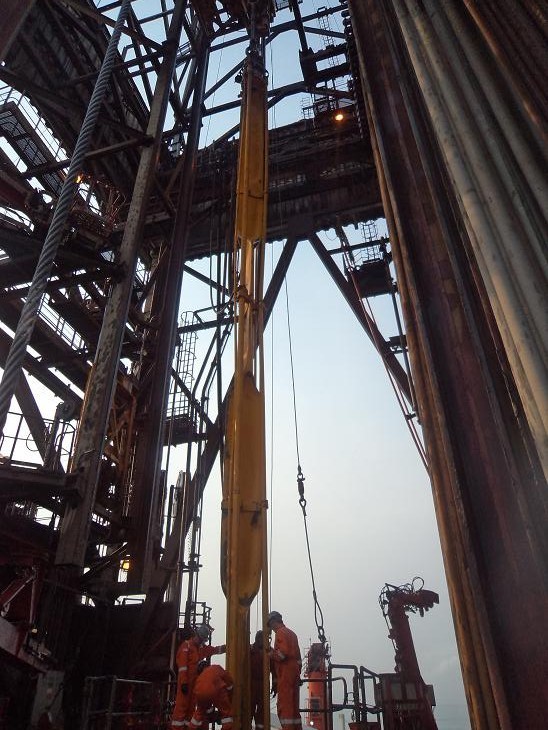
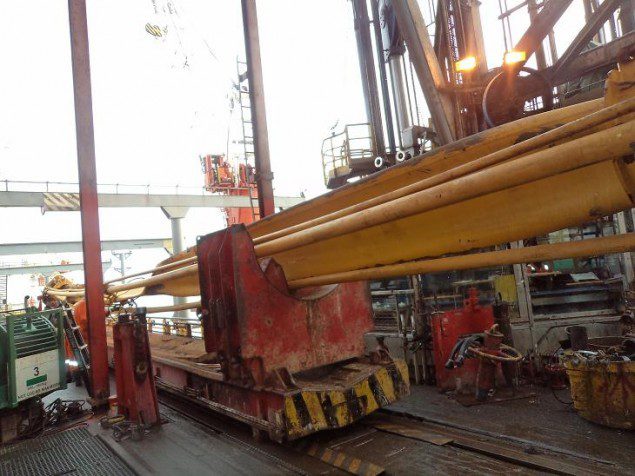
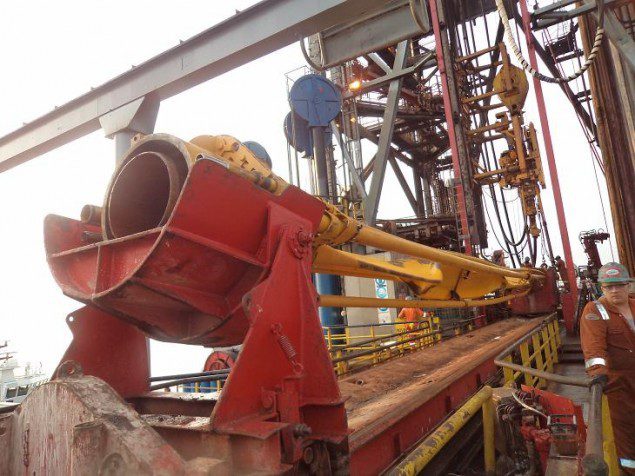
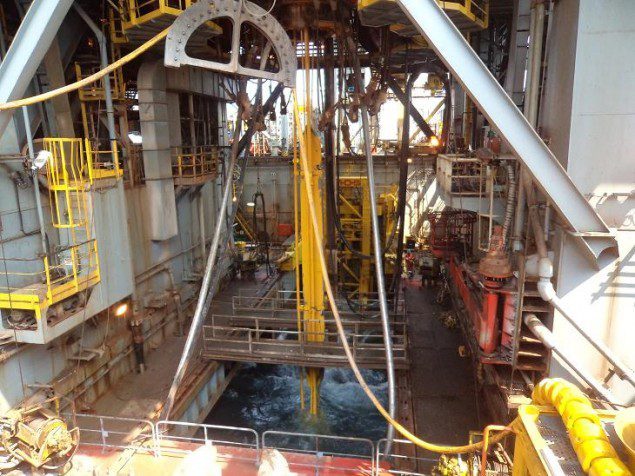


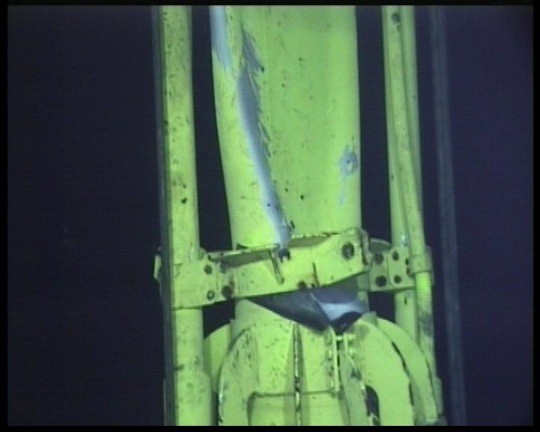


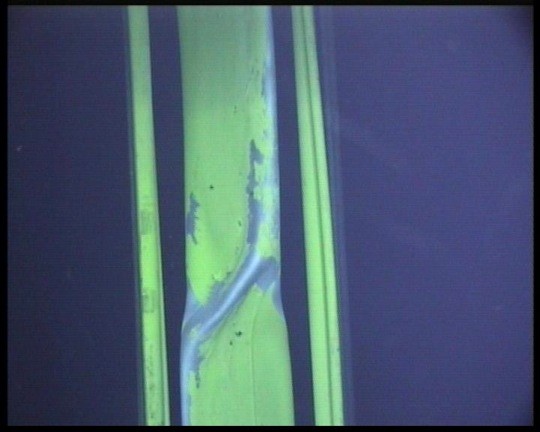

After discovering the failure on their ROV cams, French energy major Total, which had contracted the rig, continued to lower the BOP to the wellhead where the BOP was made up, and the Lower Marine Riser Package (LMRP) was unlatched and brought to the surface. The collapsed riser joints were then replaced.
The deepwater drilling process in a very small nutshell
When drilling a deepwater well, the drilling rig will “spud in” or begin drilling, with large rock bit (the ones with big teeth on them), perhaps 26 inches in diameter, and it will drill (nozzle) a few hundred feet down in order to set the 30 or 36 inch conductor casing, which is the biggest and heaviest-walled casing string that is lowered into the well. This string is lowered at the same time as the drill bit is nozzle-ing into the mud.
After it’s set, the top section of the well is drilled to a certain point, perhaps a few thousand feet down depending on the geology, where the well is then cased off using a 22 inch steel pipe.
This casing string forms the high pressure wellhead, which is locked into the low pressure wellhead (the 30″ or 36″) and subsequently cemented into place.
After the 22 inch wellhead is in place, the blowout preventer (BOP) with an 18 3/4 inch inside diameter (ID) is lowered down to the wellhead and locked into place.
From then on, oil-based mud is used to drill progressively narrower holes down into the earth while the cuttings are captured and the mud is recirculated down into the well via the center of the drill pipe.